Understanding Precision CNC Machining and Its Suppliers
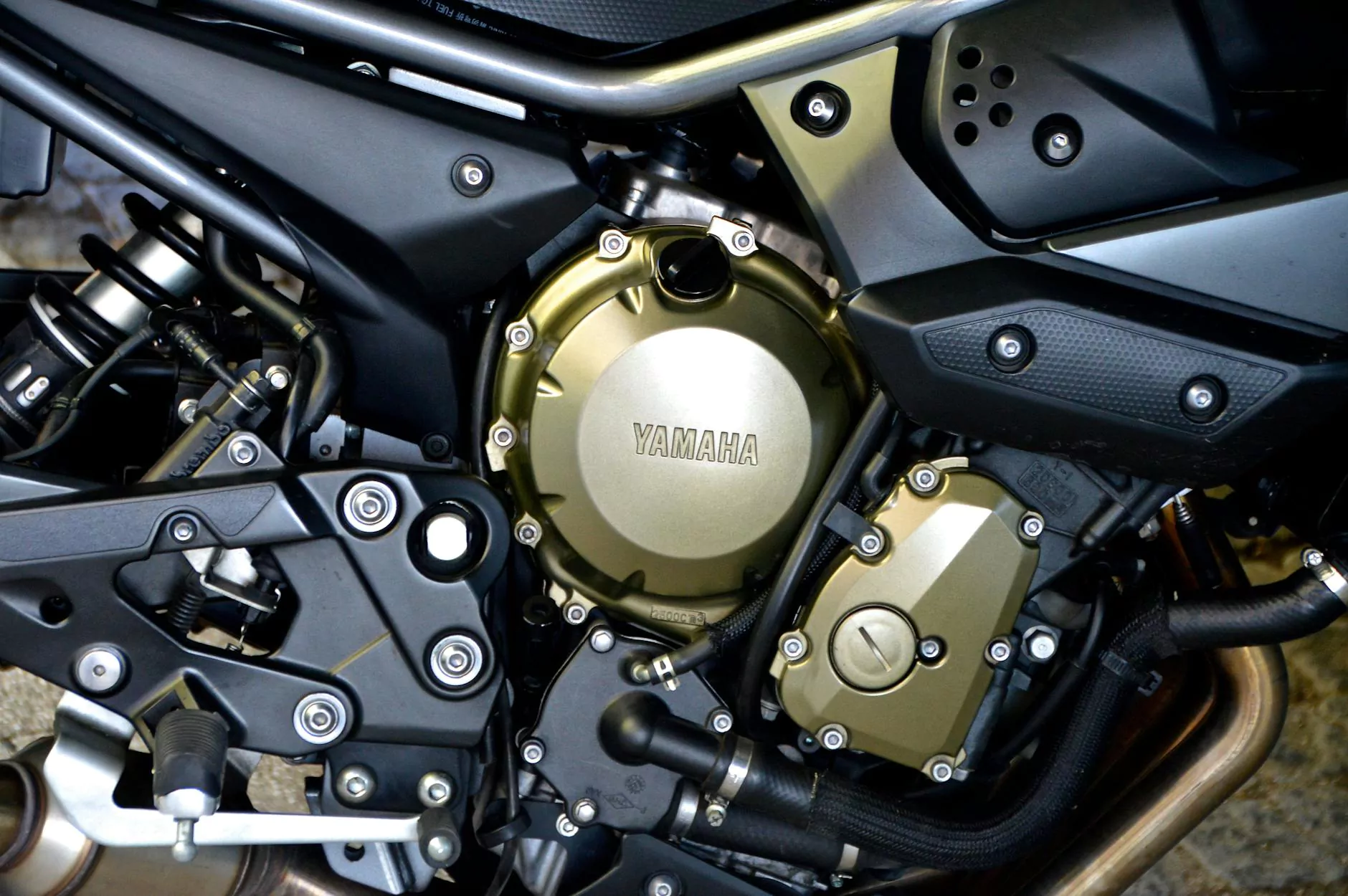
In today’s competitive manufacturing landscape, the role of a precision CNC machining supplier cannot be overstated. Companies rely on precision machining for the production of intricate components required in various industries, from automotive to aerospace. This article delves into the intricacies of CNC machining, why selecting the right supplier matters, and how it impacts your business operations.
What is Precision CNC Machining?
CNC stands for Computer Numerical Control, which involves the use of computer systems to control machine tools. Precision CNC machining is a process used to create parts by removing material with high accuracy. This technique allows for:
- Complex geometries that traditional machining methods cannot achieve.
- Minimized waste of raw materials through efficient production techniques.
- High repeatability ensuring that each part meets strict specifications across multiple production runs.
The Role of a CNC Machining Supplier
A reliable precision CNC machining supplier plays a crucial role in the manufacturing process. The supplier is responsible for providing not only the machinery and technology but also the expertise required to optimize production. This includes:
- Technical support to assist with CNC programming and process improvements.
- Quality assurance measures to ensure parts meet industry standards.
- Logistical support to facilitate timely delivery of components.
Advantages of Working with a Precision CNC Machining Supplier
Choosing the right precision CNC machining supplier can lead to numerous advantages for your business, including:
1. Enhanced Production Efficiency
A proficient supplier can streamline your manufacturing processes, resulting in faster turnaround times. This efficiency translates into reduced production costs, allowing for competitive pricing of your products.
2. Consistent Quality Control
Quality control is vital in manufacturing. A reputable supplier employs rigorous inspection processes, ensuring that every part meets specified tolerances and quality standards. This consistency helps build trust with your customers.
3. Access to Advanced Technology
The machining industry is continually evolving, with new technologies emerging that improve accuracy and efficiency. Partnering with a top-tier precision CNC machining supplier gives your business access to the latest advancements, ensuring you remain competitive.
Key Factors to Consider When Choosing a Precision CNC Machining Supplier
Not all suppliers are created equal. When selecting a precision CNC machining supplier, consider the following factors:
1. Industry Experience
Look for suppliers with a proven track record in your specific industry. An experienced supplier will understand the unique challenges and requirements of your field, ensuring better service and outcomes.
2. Capabilities and Equipment
Examine the machining capabilities of the supplier, including the types of materials they can work with and the precision levels they can achieve. Ensure they have state-of-the-art equipment that aligns with your production needs.
3. Customer Support
Strong customer support is essential for maintaining a successful partnership. Your supplier should offer technical assistance, prompt responses to inquiries, and solutions to any challenges that arise during the manufacturing process.
4. Quality Certifications
Verify that the supplier holds relevant quality certifications, such as ISO 9001, which reflects their commitment to maintaining high-quality standards in their operations.
Impact of CNC Machining on Various Industries
CNC machining is versatile and finds applications in numerous sectors. Some notable industries that benefit from precision CNC machining include:
- Aerospace: Precision components that meet stringent safety regulations.
- Automotive: High-volume production of intricate engine parts.
- Medical: Manufacturing of highly precise surgical instruments and implants.
- Electronics: Production of components that require fine tolerances for functionality.
- Robotics: Parts that enable advanced automation and control.
Future Trends in Precision CNC Machining
As technology continues to evolve, the future of precision CNC machining looks promising. Here are some trends to keep an eye on:
1. Integration of AI and Machine Learning
The incorporation of artificial intelligence in CNC machining is set to revolutionize the production process by predicting maintenance needs, optimizing machining parameters, and enhancing quality control measures.
2. Increase in Automation
Automation reduces labor costs and increases production efficiency. Suppliers that invest in automated machining systems will offer significant advantages over competitors.
3. Sustainability Practices
With growing environmental concerns, companies are turning to sustainable machining practices. This includes minimizing waste, recycling materials, and using eco-friendly coolant options in machining processes.
4. Customization and Flexibility
Customers increasingly demand customized solutions. Suppliers that offer flexible machining options and quick turnaround times for small batches will be better positioned in the market.
Conclusion
Selecting the right precision CNC machining supplier is a critical decision that can significantly influence your production capabilities and overall business success. By considering the supplier’s experience, capabilities, support, and quality certifications, you can ensure that your manufacturing processes run smoothly and effectively. As the industry continues to grow and evolve, staying informed about trends and advancements will position your business for long-term success. For high-quality precision machining services, you can trust the expertise at Deep Mould to meet your manufacturing needs.