The Ultimate Guide to Silicone Membranes and Their Applications
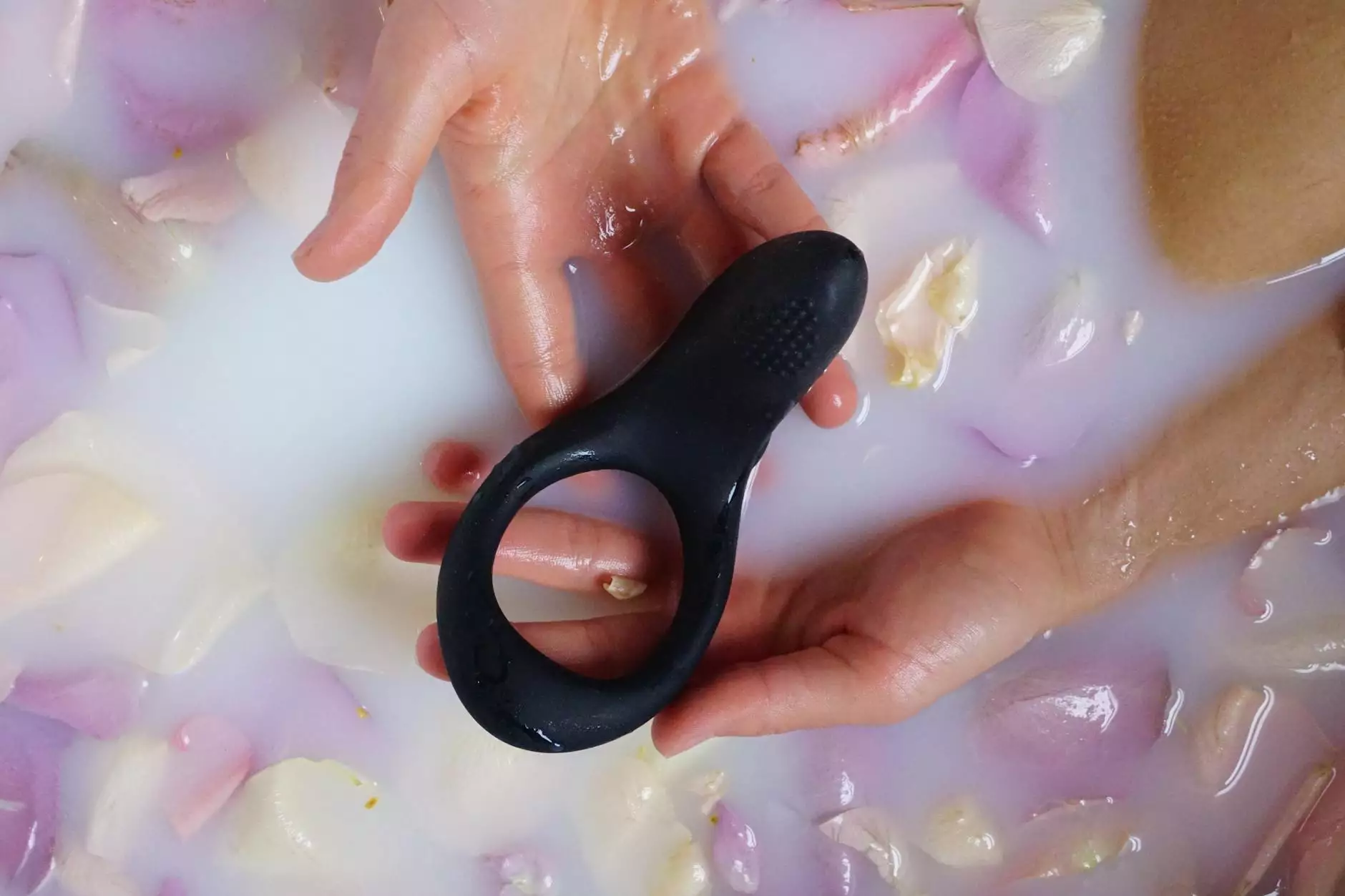
In the dynamic world of industrial applications, the demand for innovative materials has reached new heights. Among these materials, silicone membranes have emerged as a favored choice in various sectors, thanks to their unique properties and versatility. This article will delve deep into the fascinating world of silicone membranes, examining their composition, advantages, and wide-ranging uses. By the end of this guide, you will have comprehensive knowledge about silicone membranes and their vital role in modern technologies.
What Are Silicone Membranes?
Silicone membranes are flexible, durable sheets made from silicone rubber. These membranes can endure extreme temperatures and harsh environments, making them ideal for various industrial applications. Their unique chemical structure provides excellent resistance to heat, ozone, oxidation, and UV radiation, ensuring longevity even in challenging conditions.
Composition of Silicone Membranes
The primary component of silicone membranes is silicone polymer. This polymer is renowned for its elasticity, making it an excellent choice for applications requiring flexibility while maintaining strength. Silicone membranes can come in various forms, including:
- Solid Silicone Membranes: Ideal for applications that demand high durability.
- Foamed Silicone Membranes: Used where cushioning or insulation is needed.
- Perforated Silicone Membranes: Suitable for applications requiring airflow or drainage.
Advantages of Silicone Membranes
When selecting materials for industrial use, silicone membranes stand out for many reasons:
1. Exceptional Temperature Resistance
Silicone membranes can handle extreme temperatures ranging from -60°C to +230°C. This characteristic makes them particularly useful in environments where other materials would fail.
2. Chemical Stability
Silicone membranes show remarkable resistance to various chemicals, oils, and solvents, which is essential for industries such as automotive and pharmaceuticals.
3. Long Lifespan
Due to their inherent durability and resistance to wear and tear, silicone membranes often outlast other materials, providing excellent value over time.
4. Flexibility
The high elasticity of silicone membranes enables them to conform to different shapes and surfaces, making them ideal for use in vacuum systems and other applications requiring adaptability.
5. Health and Safety
Silicone is a non-toxic material that meets stringent safety standards. This makes silicone membranes suitable for applications in the food, medical, and dental fields where hygiene is paramount.
Applications of Silicone Membranes
Silicone membranes have found their way into an extensive range of applications. Here are some of the most notable:
1. Vacuum Systems
In the realm of vacuum systems, silicone membranes are essential components for creating seals and controlling airflow. Their ability to maintain integrity under vacuum pressures makes them invaluable in various industrial operations.
2. Medical Devices
Many medical devices utilize silicone membranes due to their biocompatibility and ability to withstand sterilization processes. Applications include ventilators, infusion pumps, and drug delivery systems.
3. Automotive Seals
In the automotive industry, silicone membranes are used in seals and gaskets where resistance to extreme temperatures and chemical exposure is critical for reliability and safety.
4. Food Processing Equipment
The food industry benefits from silicone membranes for their non-reactive properties, ensuring that food safety standards are met during processing and packaging.
5. Aerospace Components
Silicone membranes are used in the aerospace sector for their lightweight and resilient characteristics that help in demanding environments such as high altitudes and varying temperatures.
Buying Silicone Membranes: Key Considerations
When considering the purchase of silicone membranes, it's essential to factor in several aspects to ensure you choose the right product for your needs.
1. Application Requirements
Identify the specific requirements of your application, including temperature range, chemical exposure, and durability. This will guide you in selecting the most suitable silicone membrane.
2. Thickness and Dimensions
Silicone membranes come in various thicknesses and sizes. Ensure that the dimensions meet your design specifications for optimal compatibility and performance.
3. Certification Standards
For applications in sensitive industries such as food or medicine, look for silicone membranes that comply with relevant safety and quality certifications.
4. Supplier Reputation
Choosing a reliable supplier like vacuum-presses.com, known for high-quality silicone membranes and excellent customer service, can impact the success of your project.
5. Cost vs. Quality
While it may be tempting to opt for the cheapest option, investing in a high-quality silicone membrane ensures better performance and longevity, ultimately saving you money in the long run.
Conclusion: The Future of Silicone Membranes in Industry
As technology continues to advance, the role of silicone membranes in various applications will only grow. Their unique properties make them a cornerstone in industries ranging from healthcare to automotive, highlighting the need for innovative materials as the backbone of modern manufacturing processes. By understanding their benefits, applications, and buying considerations, businesses can make informed decisions that will enhance their operational efficiency.
For more information or to purchase high-quality silicone membranes and other vacuum system parts, visit vacuum-presses.com, where you can explore a variety of options tailored to your specific needs.