CNC Lathe Machining Parts Factory: A Deep Dive into Precision Engineering
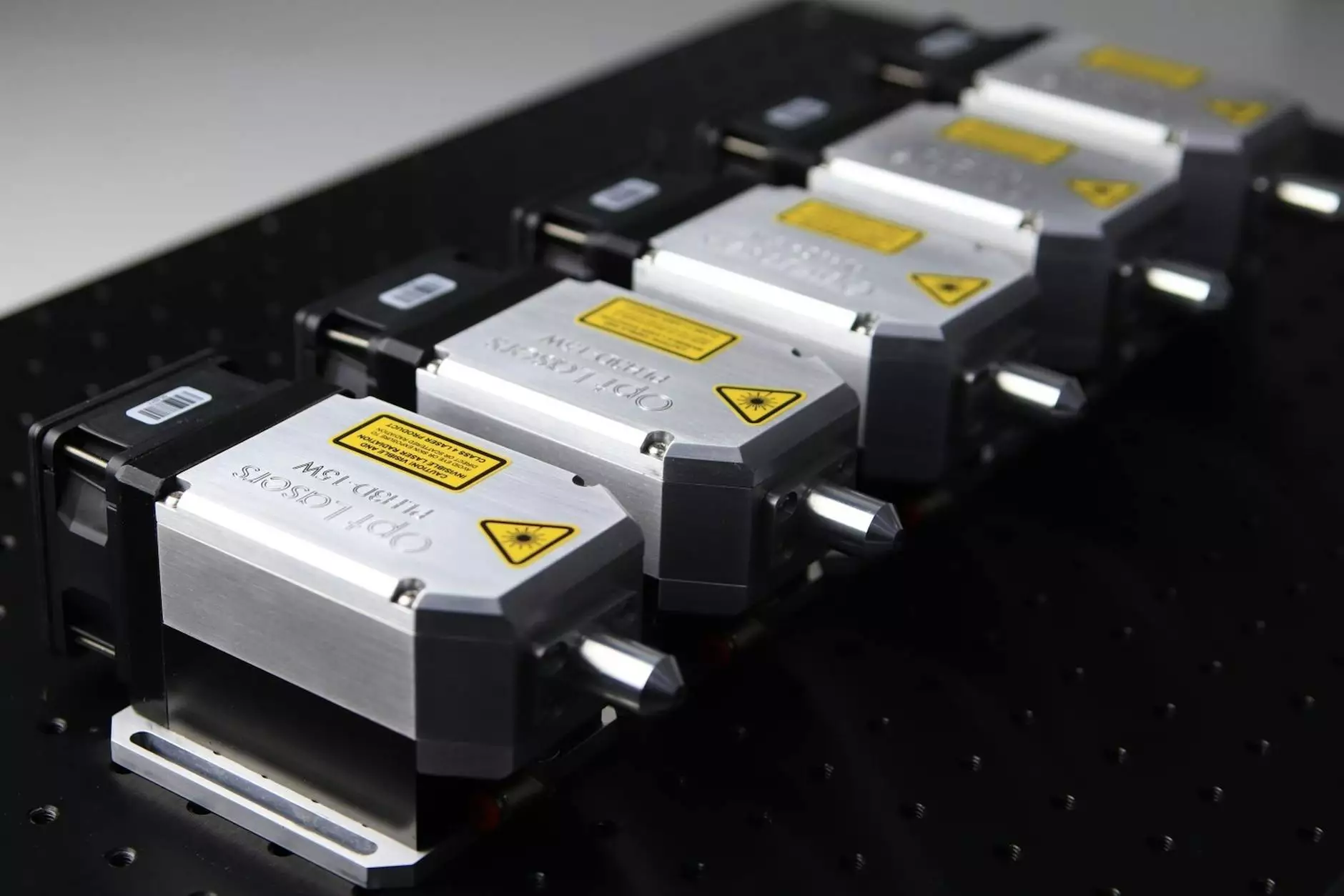
In the contemporary manufacturing landscape, the role of a cnc lathe machining parts factory is pivotal. With the demand for high-precision components on the rise across various industries, understanding the intricacies of CNC (Computer Numerical Control) lathe machining is essential for businesses seeking efficiency and excellence. This article unveils the critical aspects of CNC lathe machining, its processes, benefits, and how factories like deepmould.net excel in providing top-notch services.
Understanding CNC Lathe Machining
CNC lathe machining is a sophisticated manufacturing process that involves the use of computer-controlled machines to fabricate parts from solid materials, such as metal or plastic. The cnc lathe operates by rotating the workpiece against a stationary cutting tool, allowing for precise shaping and detailing of components.
Key Components of CNC Lathe Machining
At the heart of CNC lathe machining are several critical components, each playing a vital role in the process:
- CNC Controller: The brain of the lathe, which interprets the CAD/CAM design and executes the machining instructions.
- Spindle: This component holds and rotates the workpiece, allowing for various machining operations.
- Tool Holder: Secures the cutting tools in place, enabling them to perform precise cuts.
- Bed and Carriage: Provide stability and support for the machine and its components.
- Power Supply: Supplies energy to drive the lathe and its functions.
The Processes Involved in CNC Lathe Machining
The CNC lathe machining process encompasses several stages, each requiring meticulous planning and execution. Here is a breakdown of the typical workflow:
1. Design and Programming
The first step involves creating a detailed design using CAD (Computer-Aided Design) software. This design is then converted into a CNC program using CAM (Computer-Aided Manufacturing) software. The program dictates the specific movements and actions the lathe will undertake.
2. Material Selection
Selecting the right material is crucial as it affects the durability and functionality of the finished product. Common materials used in CNC lathe machining include:
- Aluminum
- Brass
- Mild Steel
- Stainless Steel
- Plastics
3. Setup and Machining
Once the design and materials are ready, the machinist sets up the CNC lathe, installing the necessary tools and fixtures. The machining process follows, where the lathe executes the programmed instructions with remarkable speed and precision.
4. Quality Control
Quality assurance is critical in CNC machining. After the components are machined, they undergo strict quality control checks to ensure they meet the specified tolerances and standards. This may involve using measurement tools such as calipers, micrometers, and CNC CMM (Coordinate Measuring Machine).
5. Finishing and Delivery
After quality checks, the parts may go through additional finishing processes, such as sanding, painting, or anodizing, before final delivery to the client.
The Advantages of CNC Lathe Machining
Engaging with a cnc lathe machining parts factory offers numerous advantages:
1. Exceptional Precision and Accuracy
The integration of computer control ensures ultra-high precision, which manual machining cannot achieve. Parts produced are replicable and dependable, a critical requirement in industries such as automotive and aerospace.
2. Enhanced Efficiency
CNC lathe machines operate at rapid speeds and can run 24/7, significantly reducing production time and labor costs.
3. Flexibility in Production
CNC lathes can easily switch between different projects without requiring extensive downtime for retooling, making them adaptable to a variety of production runs.
4. Reduction of Material Waste
With precise machining capabilities, CNC machining minimizes material waste, providing a cost-effective solution while promoting environmentally sustainable practices.
5. Safe and Consistent Operations
Automation of machining processes leads to safer working conditions and minimizes the risks associated with manual operations.
Industries Benefitting from CNC Lathe Machining
The versatility of CNC lathe machining has made it a critical component across various industries, including:
- Aerospace: Manufacturing precise components such as turbine blades and housing fittings.
- Automotive: Producing essential parts like shafts, gears, and housings.
- Medical: Crafting intricate surgical tools and implants with stringent quality requirements.
- Electronics: Creating casing and connectors that demand high precision and durability.
- Construction: Fabricating parts like brackets, fasteners, and fixtures that are vital in construction projects.
Choosing the Right CNC Lathe Machining Parts Factory
When seeking a cnc lathe machining parts factory, consider the following factors to ensure you partner with a reliable provider:
1. Experience and Expertise
Look for a factory with a proven track record and significant experience in CNC lathe machining. Their expertise will reflect in the quality of their work.
2. Technology and Equipment
Assess the technology and machinery they use. Advanced, up-to-date equipment can significantly affect the quality and efficiency of production.
3. Quality Assurance Processes
Inquire about their quality control measures and certifications. A factory that adheres to recognized standards ensures higher reliability and performance.
4. Customer Support and Communication
Effective communication and customer support are essential. Choose a factory that values transparency and keeps clients updated throughout the production process.
5. Competitive Pricing
While cost is a factor, it should not be at the expense of quality. Evaluate the pricing structure and find a balance that offers value for money.
Future Trends in CNC Lathe Machining
As technology continues to evolve, several trends are on the horizon for CNC lathe machining:
1. Increased Automation
The future will likely see higher degrees of automation in manufacturing, reducing human intervention and errors while enhancing efficiency and safety.
2. Integration of Artificial Intelligence
AI can optimize machining processes by predicting failures, improving tool life, and enhancing overall operational efficiency.
3. Advanced Materials
As new materials are developed, CNC lathes will adapt to machining more complex and durable compounds, expanding their applications.
4. IoT Implementation
The Internet of Things (IoT) will lead to smarter manufacturing environments where machines communicate with each other, enabling predictive maintenance and rapid adjustments in production.
Conclusion: The Future of Manufacturing with CNC Lathe Machining
The importance of a cnc lathe machining parts factory in the modern manufacturing realm cannot be overstated. With its proven benefits of precision, efficiency, and versatility, CNC lathe machining will continue to be at the forefront of engineering solutions across industries. By choosing a reputable factory like deepmould.net, businesses can assure the quality and reliability of their components, paving the way for sustained success and innovation in their respective fields.
Embrace the future of manufacturing and ensure your parts are produced with cutting-edge technology, expertise, and meticulous attention to detail. Join the growing list of companies that rely on CNC lathe machining to remain competitive in today's fast-paced marketplace.